“As a long-standing customer of Lestercast, I always receive a first-class service from a responsive and highly experienced team”.
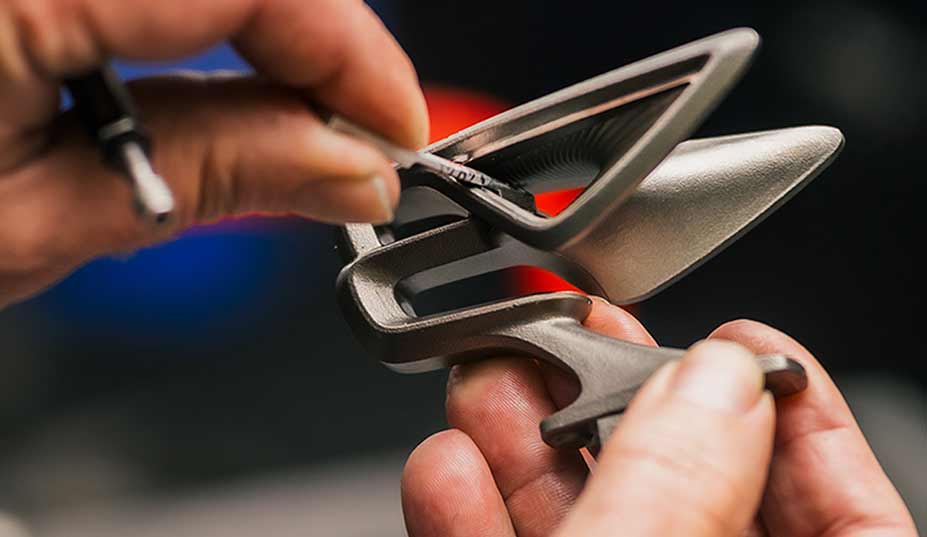
Investment Casting
Lestercast is a leading UK Investment Casting manufacturer, supplying major OEM’s and suppliers across all industries and around the world, for over 50 years. We offer high quality bespoke castings in Steel, Stainless Steel, Aluminium, Nickel & Cobalt Superalloys, Brass & Bronze & Zinc.
By providing innovative solutions, quality products and excellent service, we deliver a ‘complete investment casting package’. Lestercast pride ourselves with an excellent on-time delivery performance and also offer on-site stock holding facilities. We are able to offer our customers high quality castings manufactured in our foundry in Leicestershire, as well as from our partner facility overseas.
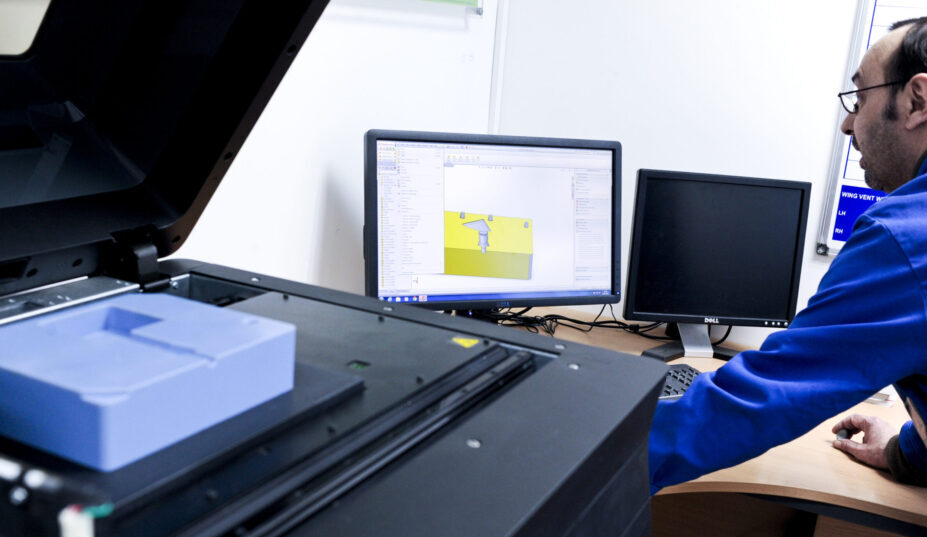
Rapid Prototyping
As a pioneering UK Investment Casting specialist, Lestercast can provide customers with an efficient, no tool, “Rapid Prototyping” method of acquiring high quality, investment cast parts, in a quick time.
Our highly skilled and experienced team can manufacture 3D printed wax patterns using Additive Manufacturing Technology, quickly and efficiently from customer approved 3D CAD geometry.
Reducing the manufacturing lead-time, allows prototype castings to be tested and verified prior to commencing with any production tooling.
We Have The Latest Technology….
MAGMASOFT® Simulation Software
We have the latest technology on hand, including simulation software, to make sure that your investment casting project runs as smoothly as possible from design through to delivery.
The Investment Casting process has benefited many industries as an economical route to cast near-net-shape metal parts with high geometric complexity and dimensional accuracy. However, the manufacturing costs and lead-times during production can quickly limit the competitiveness of investment casting as the preferred manufacturing route. Lestercast use MAGMASOFT® investment casting simulation software as a virtual prototyping tool for eliminating physical casting trials. Therefore improving investment casting quality which significantly reduces production costs and time.
Magmasoft is a brilliant scrap prediction and prevention tool. It shows the user how and why an investment casting method may or may not work by providing a variety of result types. Collating this information and applying our extensive knowledge and experience we can ensure the best possible design of casting method is being used before any tools have been cut or any waxes have been produced.
Some benefits of investment casting simulation:
- Detecting areas of concern with a casting design.
- Reduction of scrap
- Continuous improvement of casting quality
- Shorter production times
- Predicts filling and solidification behaviour during the casting process.
Reverse Engineering:
At Lestercast, our in-house 3D scanner allows us to scan parts which have no CAD available. We are able to import the 3D scanned CAD model into MAGMASOFT® simulation software, enabling us to produce the highest quality investment castings in the most cost effective way.
Did you know….Investment Casting is also known as Lost Wax Casting & Precision Casting?
If you would like to learn more about the investment casting process please visit our investment casting process page. You can also go to our about us page and watch our corporate video, where you are introduced to some of the team, learn about our investment casting services and watch some of the investment casting process at our facilities in Leicestershire.
We produce over 1 million parts annually for 170 different global companies, using over 100 metal specifications, across 20 different industry sectors.
CDP as Standard
All new products come with a Component Development Plan as standard.
This is an ongoing report where customers are kept up to date with the progress of their new investment castings, whether it be manufactured at our foundry in the UK or manufactured in our overseas partner foundry.
Our customers receive an itemised schedule and timeline for their order, which is updated at key stages of the manufacturing process. Updates also include photographs and any relevant documentation specific to the order.
If you would like to view a typical Component Development Plan, please click on the image (right).
What Our Customers Say About Us……
“Lestercast continues to be one of our most suppliers.”
Senior Buyer
“Lestercast has always been very attentive to any request sent.”
(Anon) Senior Buyer
“Lestercast are so easy to deal with, we have a great relationship, the communication channels are excellent. There is always somebody there to deal with our enquiries with a quick and efficient answer. Lestercast offer a stockholding facility which is a massive help to have the stock available at a moment notice, this enables us to hold minimum stock levels. Overall, a pleasure to work with.”
(Anon) Procurement Manager
“Five star communication, Five star delivery, Five star service, Five star order”.
C. Bennett.
“A nice company to do business with.”
P. Buschgens
“Excellent quality product supplied on time”
(Anon) Procurement Manager
“Great service, quality products.”
N. Wright
“Our design request was dealt with swiftly and with no hassle. Great supplier.”
C. Ward
“Thank you for making me happy!”
(Anon) Engineering Manager
“We are kept informed with regard to progress of our orders and that solubles are kept in stock, this helps lower lead times.”
C. Slenzak
“We’re really happy with the service by Lestercast. The team were really responsive and friendly, indulging our curiosity about the process with patience. It was great to see our design turn into the beautiful solid bronze end result, a really quality item produced by very skilled and knowledgeable people.”
A. Johnen
“Lestercast have been a supplier for many years and I have always found them to be reliable, competitive and suppliers of quality products”.
A. Dolling
FOLLOW US
Our Customers Across The Globe……
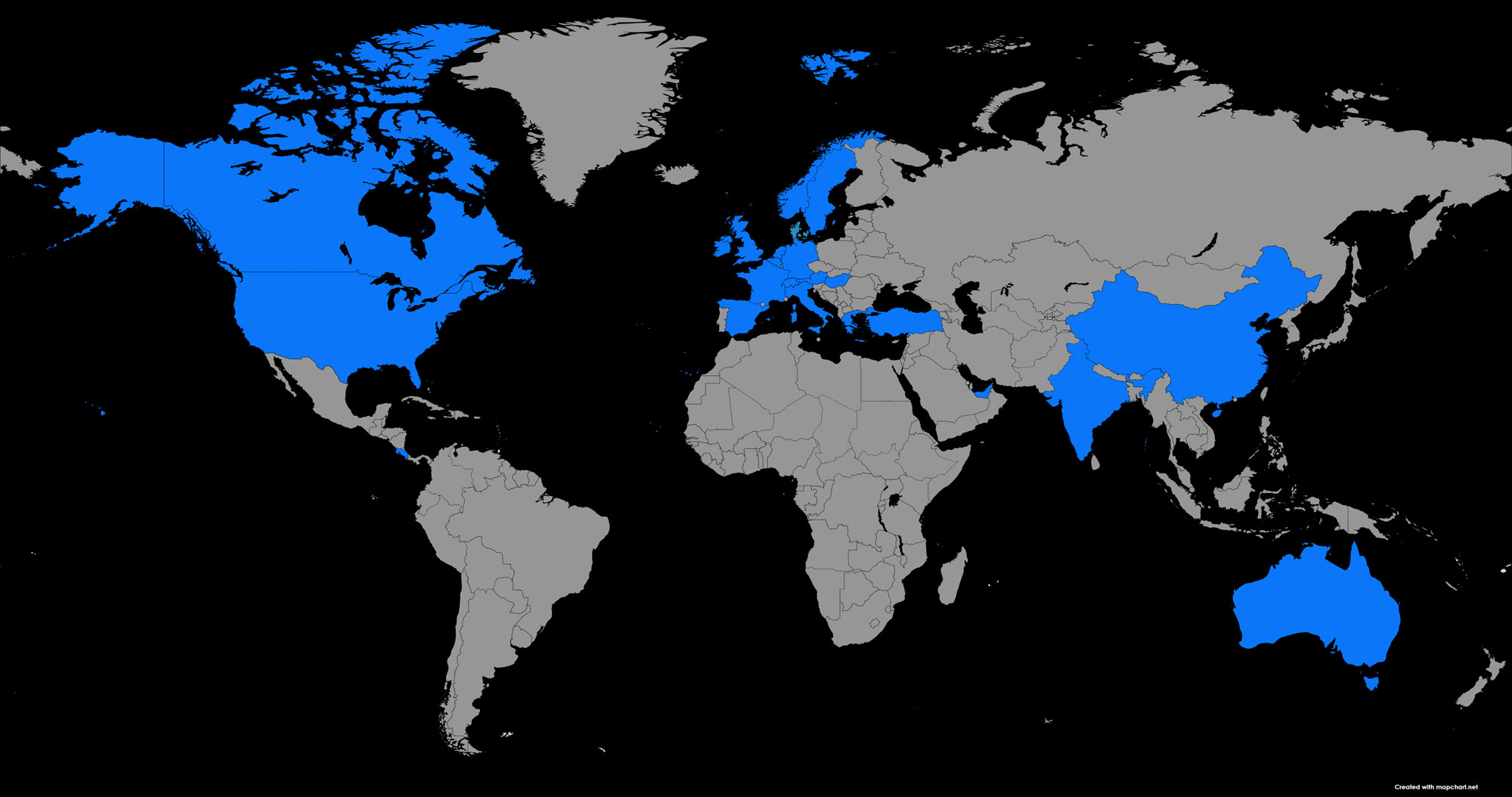